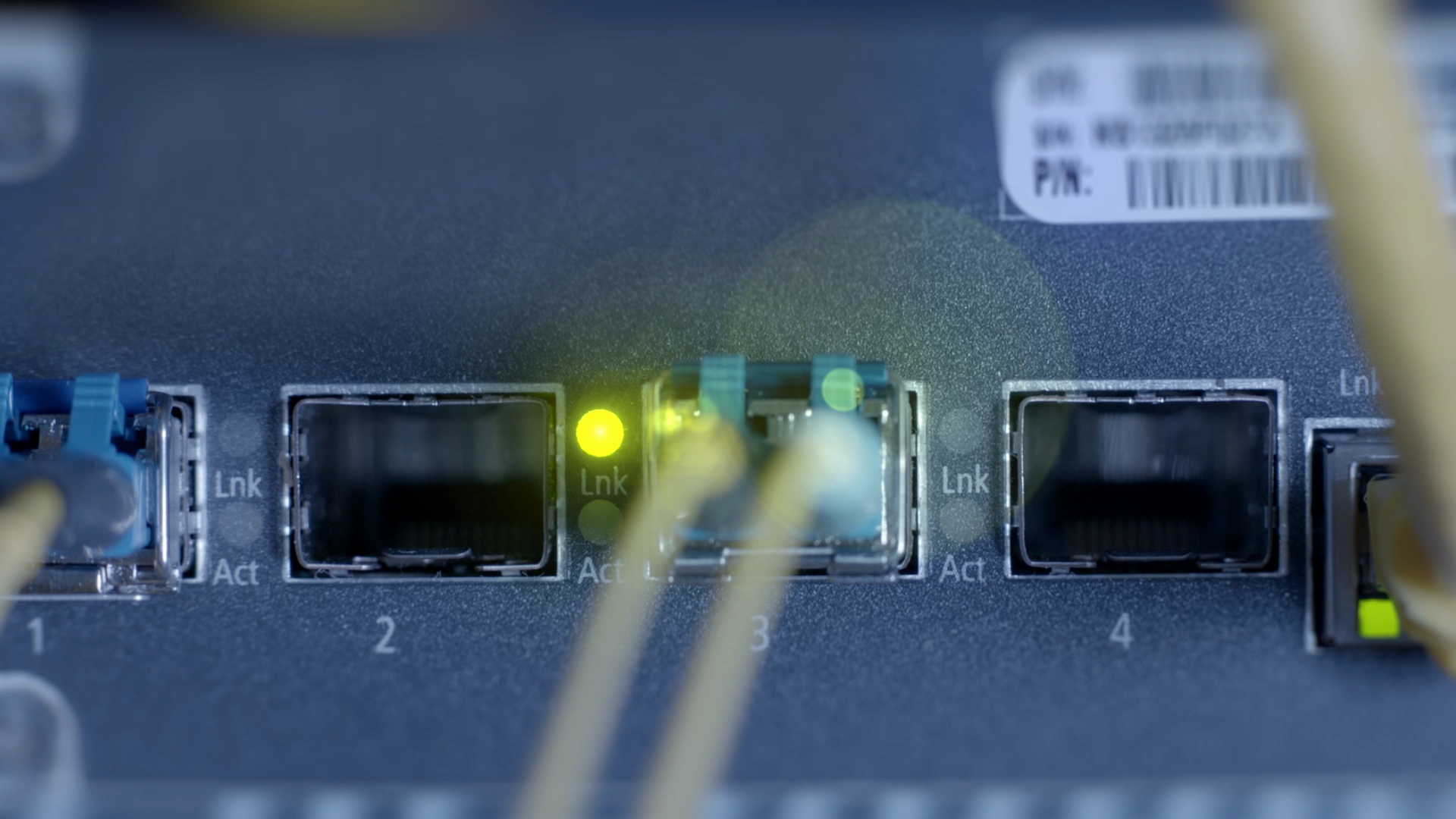
When supply chain issues threatened to delay a project for a company they were working with, SDN Communications dug deep and found a temporary fix.
Like nearly every business sector, telecommunications have been impacted by supply chain disruptions, which started when ports and factories around the world shut down due to the COVID-19 pandemic. This slowed the “movement of goods.” As the economy began to re-open, factories struggled to return to pre-pandemic operations. At the same time, consumer demand has been high.
The solution the SDN team developed works for their client, but that doesn’t make it any less frustrating for everyone involved.
For SDN, the supply chain disruptions also came on the heels of several infrastructure expansion projects.
“We have a number of projects to add capacity,” says Jake VanDewater, vice president of engineering, operations and IT. “In order to get added network in, we have to place fiber or lease the fiber.”
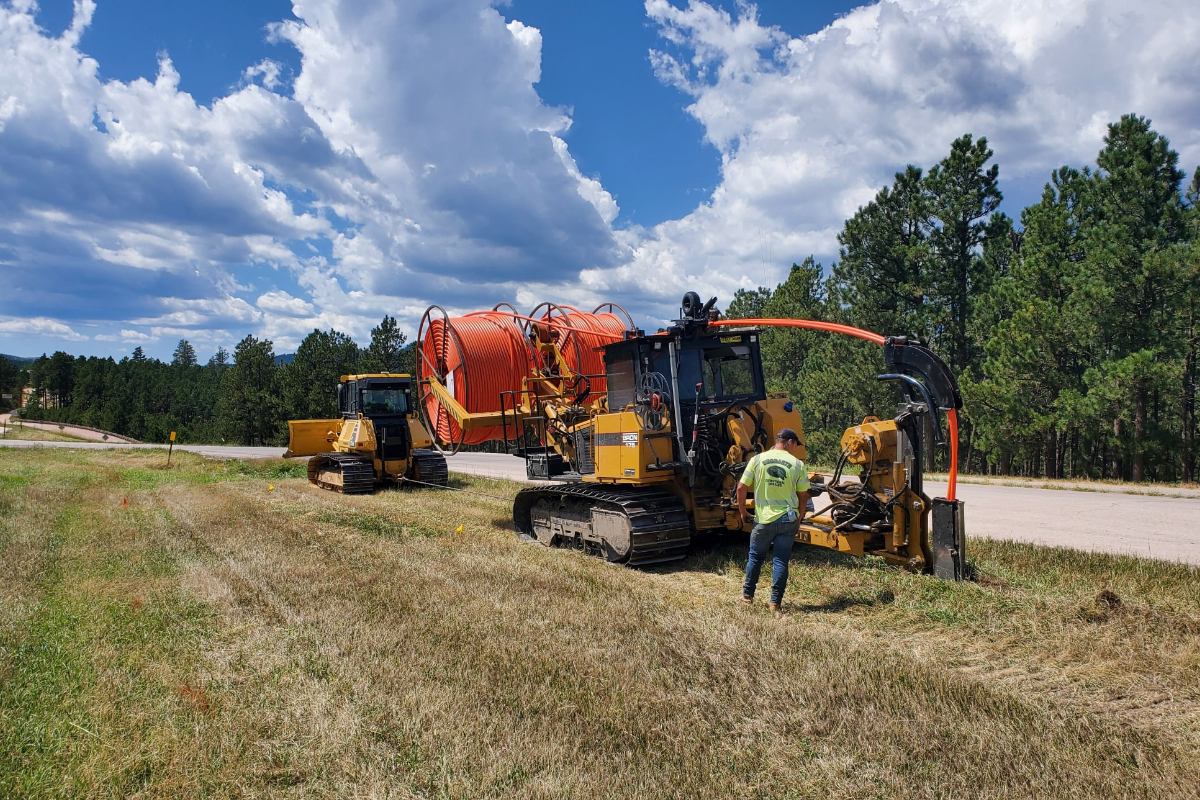
The supply chain has impacted supplies like those.
VanDewater says that while the company has adequate supply of the fiber itself thanks to forward planning, it has faced shortages of the duct or conduit that protects the fiber underground.
“Both the duct and fiber are seeing extended lead times,” he says.
A simple handhold piece, used in locations where fiber branches off, is another item that has been impacted.
“We were seeing extended lead times on getting the handholds,” VanDewater says. “We are working with a contractor to find alternative sources, but it’s caused us to push back some projects.”
Ryan Dutton, vice president of sales and marketing, says another specific area where the supply chain has impacted SDN is the shortage of firewalls.
“It’s a concern because we’ve had an uptick of interest in that space,” he says. “So far we’ve been able to meet demand.”
SDN's Managed Firewall Service monitors and defends networks from malware, attacks and data loss. SDN purchases the hardware for the firewall and then installs and supports it. They cater to medium to large companies in multiple locations.
“You’re talking about a lot of potential firewall devices for those companies,” Dutton says.
“Through luck and a little bit of foresight we’ve been able, up to this point, to mitigate this concern pretty well,” Dutton says.
But delays are still a reality.
“Companies are aware of the issue … but I don’t know if that minimizes the frustration they feel, and we feel on their behalf,” he says.
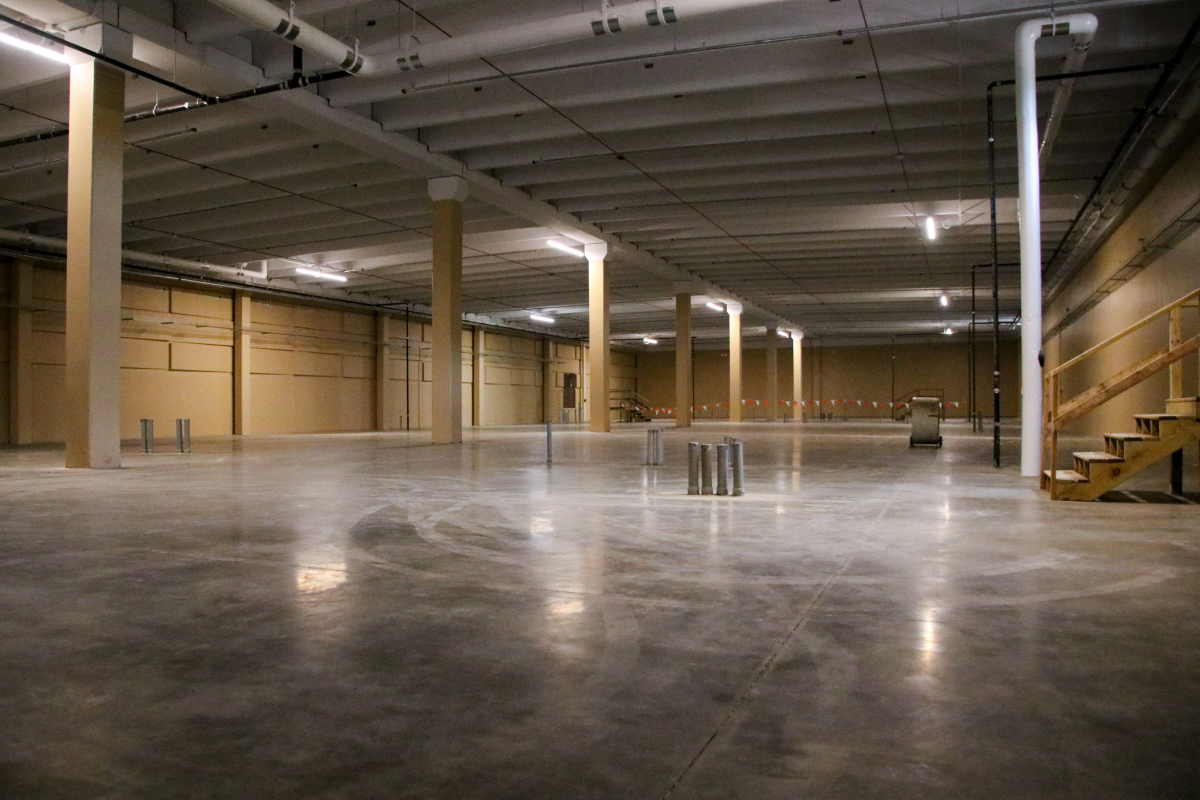
VanDewater says SDN’s 17 member companies are experiencing the same supply chain issues. Items like generators, power equipment and chiller components are impacted or delayed.
SDN Communications’ data center expansion, for example, is delayed as it waits for a chiller for the facility.
“We’re probably two to three months delayed,” VanDewater says.
Another issue for companies around the country is the labor shortage. For mid-level size companies such as SDN, it’s becoming harder to find contractors.
“There’s more money coming into our industry than ever before,” VanDewater says. “But people want the big projects. Those of us who operate at the mid to lower levels in terms of size are finding it a little harder to find that labor.”
We’re all at the mercy of our vendors, and they’re at the mercy of the manufacturers.
VanDewater says SDN remains in constant contact with vendors and continues to find alternative equipment and supplies whenever possible. Unfortunately, he doesn’t see a huge change in the situation in the immediate future.
“We’re all at the mercy of our vendors, and they’re at the mercy of the manufacturers,” VanDewater says.
Probably one of the most difficult pieces of the situation is the lack of knowing.
“It would be very different if we could provide a solid timeframe that’s realistic,” Dutton says. “It’s when you have to tell a company that we just don’t know that it’s especially frustrating. When you place an order but there’s an unknown on delivery … it can cause a little bit of a headache.”
Fortunately, the workaround that SDN was able to come up with for the Sioux Falls company has served it well. And SDN is working diligently to find needed workarounds until supply chain issues correct.